MOSFET Integrated Amplifier
This is my first attempt at building a "proper" amplifier for general use, as opposed to the Mixer-Amplifier I had made earlier. This amp was made without too much concern to cost, hence several of the approaches I've taken may be sub-optimal from the cost perspective.
Overview
- Microcontroller-controlled preamplifier, with infrared remote control capability. Volume and other settings stored in battery-backed RAM.
- LCD Display for volume, etc.
- Three general-purpose line-level inputs, one tape input, one tape output.
- 70W MOSFET-based stereo power amplifier.
- Headphone output.
- +/-38V at 4A and +/-5V at 500mA power supplies.
Microcontroller Unit (MCU)
This forms the central control secion of the amplifier. It is based on a PIC16F84A microcontroller from Microchip. The microcontroller is connected to the following peripherals:
- LM1973 μPot digital audio attenuator.
- DS1302 real-time clock (RTC).
- 2x16 character mode LCD through a 74HC163 shift register.
- CD4094 latched shift register, acting as general purpose output ports. These ports are connected to CD4052 analog multiplexers which funcion as input source selectors, tape monitor selectors and Bass Boost mode selectors. It's also connected to the LCD panel's register-select pin and the speaker muting relay driver.
- TSOP1736 IR receiver module.
- Three-button keypad.
- Headphone socket swtch, used to indicate to the MCU that headphones are plugged in, and to mute the main speakers.
The 16F84 is cheap, fast and has just the right amount of memory for the task. It does not have enough I/O ports for all functions in this application, hence I had to use serial "port extenders": using shift registers to store data sent out over an SPI-Bus style interface. SPI bus needs to be used anyway, to communicate with the RTC and the μPots.
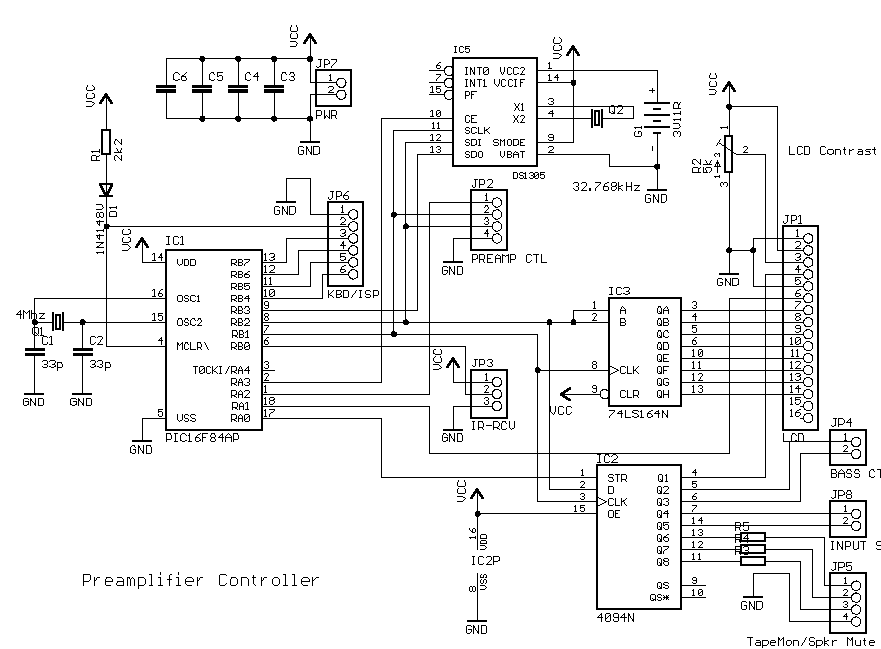
MOSFET Integrated Amp Controller Circuit
Connector JP2 goes to the μPot on the preamplifier board. The LCD connects through a standard Berg header. Some modules have a 2x8 connector in place of a 1x16, I'm not sure of the pinouts.
The 16F84 runs off a 4MHz crystal, so it can execute roughly 1 million instructions per second: more than enough for the task. It has 1k of internal Flash program memory, 64 bytes EEPROM and 68 bytes RAM. The software is written in the 16F84's assembly language, assembled with MPLAB and downloaded to the target through a home-made 16F84 programmer. The keyboard port, connected to RB7-RB4 is also used as the in-systep programming (ISP) port. To do this, the MCLR pin is also brought out to the connector. The only disadvantage with this is that programming for the keypad was difficult; you have to remove the programmer and re-connect the keypad before you could test the new changes. The software (.ASM file) is in the file preamp_ctl.zip (9kB, version 1.3). I've tried to comment parts of the code, but it's not complete. The code currently has no known bugs.
I originally intended the speaker muting relay and tape monitor ports to go to three general-purpose LEDs, hence the series resistors. They might, however, be a good idea, especially with the μPot connection, as it will serve to increase risetime, and reduce the signal coupling between the audio signals and the digital control signals.
The DS1305 RTC has a 32 kHz timekeeping crystal. It's main use is for it's 96 bytes of battery-backed NVRAM, which are used to store the current volume, input source and bass-boost selections, even when the power is removed. I could have used the PIC's EEPROM for this, but it has a limited number of write cycles. I'd either have to have a brown-out detection circuit trigger an interrupt to make the PIC write to EEPROM, or live with a limited-lifetime amplifier. Using NVRAM is easier. The MCU talks to the RTC through an SPI bus (SCLK, SDI and SDO pins). The DS1305 includes a programmable trickle-charger which can be configured through the SPI bus.
IC2 is a CD4094 shift register and latch. Data from the MCU is clocked in serially through the D and CLK pins. When the strobe pin STR receives a rising edge, the data from the shift register is internally latched and fed to the outputs. This ensures that the outputs do not change state when the MCU clocks data into or out of any of the other devices on the SPI bus (RTC, μPot, etc). IC3 is an 8-bit SIPO shift register. It behaves like the 4094, but there is no latch. This is because its outputs drive the LCD module, which has an internal latch.
Preamplifier
The Preamplifier section uses an opamp-based circuit to provide a total of +6dB gain, Volume control and two-step Bass Boost. Opamps used are the MAX414 low voltage, low-noise opamps.
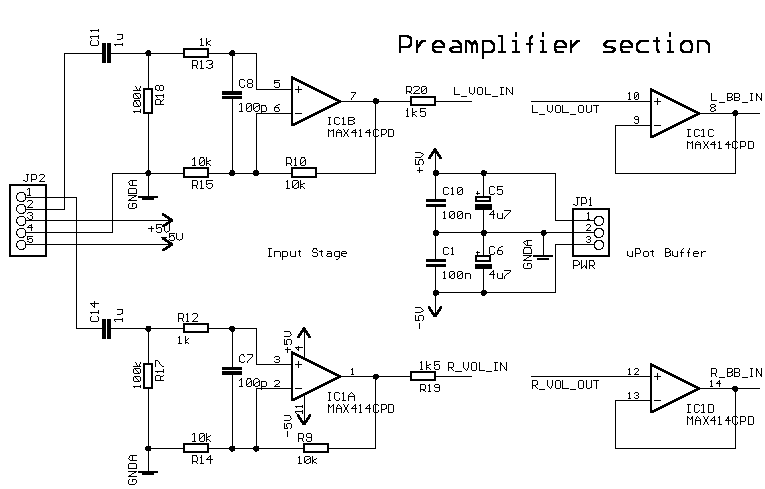
MOSFET Integrated Amp Preamplifier Input stage.
The first stage (IC1A and IC1B) uses a non-inverting amplifier configuration. Looking at the channel based on IC1B, R13 and C8 provide RF suppresion, C11 and R8 behave as an LPF, and sets the input impedance of the preamp at 100k. R10 and R15 set the gain of this stage at 2 (6dB). C1, C5, C6 and C10 provide supply bypassing. Mount C1 and C10 near the IC.
In addition to the input stage, this diagram includes a pair of buffers (IC1C and IC1D) used at the output of the μPot, which has a high output impedance.
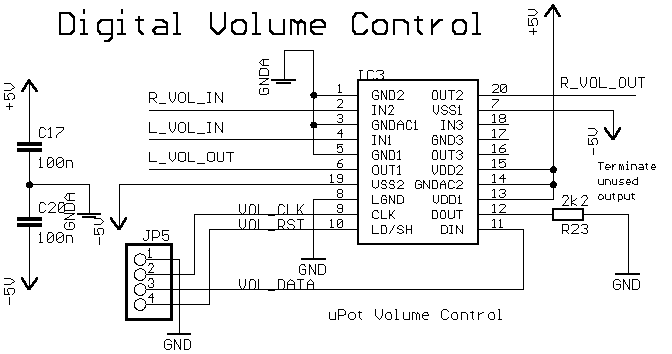
MOSFET Integrated Amp μPot
The LM1973 μPot is the digital volume control chip used in this project. It contains three digitally adjustable audio attenuators with a 78dB adjustment range, and > 100dB mute. It accepts settings changes via an SPI-bus compatible interface. In the circuit, JP5 connects to JP2 on the controller board. It has one distinct advantage over similar devices made by Dallas Semiconductor, etc. in that it uses a split supply. Thus, no exta coupling capacitors are needed to interface these to opamps.
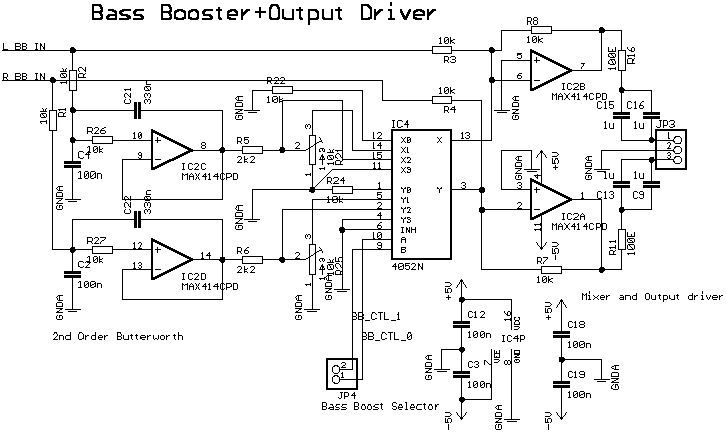
MOSFET Integrated Amp Bass Boost and Driver
The Bass Boost section provides two switchable levels of Bass enhancement. The input audio is first low-pass filtered by a second-order LPF, whose cutoff frequency is 100Hz. The LPF is built around IC2C and IC2DThe output of the LPF is given to a MUX based on a CD4052. This mux can choose between ground, an attenuated version of the LPF, and the full LPF output. The selected MUX output is summed with the original audio, yeilding a Bass Boosted signal. The outputs of this section are fed to the final power stage.
The trimpots R21 and R25 are used to set the bass level for the low-bass mode. This is usually not just the midpoint (50%) level, it's somewhere like 70%. It can be adjusted to personal taste. IC2A and IC2B act as the summing amplifier and output stage driver. 100Ω resistors R11 and R16 are used to prevent the load capacitance from causing instability in IC2A and IC2B. 2μF coupling capacitance is provided.
Input Selector
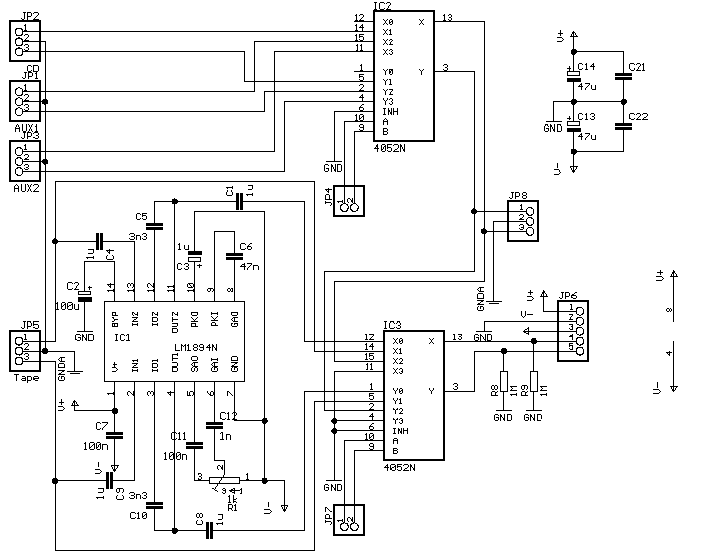
MOSFET Integrated Amp Input Selector
The Input Selector is built around two CD4052 analog multiplexers. IC2 is used to select the input source (CD/AUX1/AUX2) and IC3 is used to choose either the source selected above, the tape monitor or the tape monitor after noise reduction using National Semiconductor's LM1894 Dynamic Noise Reduction (DNR) chip. The DNR section is built around IC1, and is discussed on this page. JP1-3 are the source inputs, JP5 is the tape monitor input. R1 adjusts the DNR level. This is adjusted while listening to a soft passage to just above the point where the quietest part of the programme material "drops out". JP4 and JP7 come from the MCU board and are used to select the inputs and tape monitor. JP8 is the tape-out port, and has the currently selected input. It is not buffered, but it should be. JP6 is the connection to the preamp board (both power and signal). 1MΩ resistors are provided to ensure that the input capacitors of the preamp do not cause popping when inputs are switched from one source to the other.
Headphone Amplifier

MOSFET Integrated Amp Headphone Amplifier
The headphone amplifier is based on National Semiconductor's LM4880 headphone amplifier chip. It reduces the size of the headphone amp used.
Power Amplifier
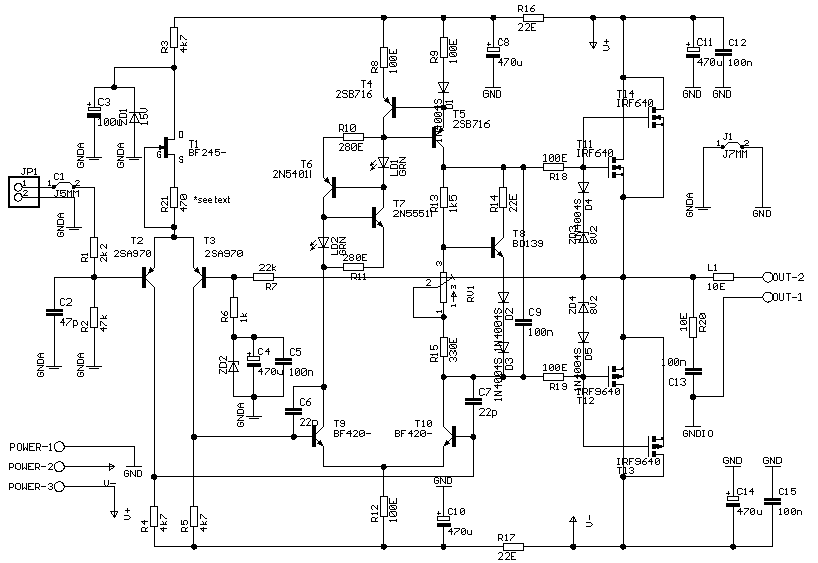
MOSFET Integrated Amp Power Amplifier
This circuit is from David White's article in Electronics World (August 2001). It uses inexpensive HexFet™ Power MOSFETs as output devices. Since their transconductance is low, the rest of the design is geared towards producing maximum open-loop gain. Overall Negative Feedback is used to set the gain to 27dB and to reduce the distortion.
The input devices used (2SA970) are low-noise, high gain PNP devices. They have poor Vce(max), so their supply voltage is reduced using a simple Zener diode regulator built using R3, ZD1 and C3. T1 is used as a current source. The author of the original EW article mentioned using a plain gate-source connected JFET, which is selected to produce 1mA current. At Rs. 25 a pop, I was not about to do this with BF245s. Besides, the current for my G-S connected BF245s is around 7mA. Insert a resistance in series with the source to reduce the current. Since the source-drain current is dependent on the manufacturing process, you should select the resistor for each BF245 in a multiple-amp. system. The value should be selected for 1mA current. If required, use a 1k pot here.
C1 forms the input blocking cap, but is shorted with a jumper because the blocking capacitor is already present on the preamp board. R1 and R2, together with C2 form an RF suppression network at the input. R2 sets the input impedance at 47kΩ. R4 and R5 are the collector loads for T2 and T3. I found that using a current mirror did not improve the THD rating of the amp (at least in Spice), so I dropped that idea. ZD2 (A 2.7V Zener), C4 and C5 prevent the base of T4 from getting beyond 2.7V in the event of amplifier clipping, output device failure, etc.
T9 and T10 forms the voltage amplifer stage (VAS). The original circuit recommended using 2SD756 transistors, which I couldn't find. The BF420 is similar, with slightly lower beta. It's a differential stage, with a constant current source formed by T6, T7, LD1, LD2, R10 and R11. A Wilson current mirror, formed by T4, T5, D1, R8 and R9 acts as the collector load for T9 and T10, ensuring maximum gain. T8, R13-15, RV1 D2 and D3 form the voltage offset between the gates of the output devices, to bias them into Class AB operation. RV1 sets the bias current. T8 should be in thermal contact with the output devices. R10 and R19 are used to limit the current drawn by the gate capacitance of the output devices. C6 and C7 form the Miller capacitors. Remember that you will need to change this if any of the transistors are substituted with different ones. I used styroflex capacitors here. R16, R17, C8 and C10 act as LPFs to filter the supply to the VAS and input stage.
D4, D5, ZD3 and ZD4 form a rudimentary short circuit protection for the output MOSFETs. It will limit the current long enough for the supply fuses to blow. C11, C12, C14 and C15 are supply decoupling capacitors. C12 anc C15 should be placed near the MOSFET drains. C13 and R20 form the Zobel network, used to compensate for the speaker coil's rising impedance with frequency. L1 is a 10 ohm, 1W resistor with around 10 turns of enamelled wire wrapped around it, connected in parallel. This is used to prevent the speaker cable capacitance from causing amplifier instability. The circuit shown uses two paralleled MOSFETS, although this is not required; it just gives addiional stability. It may be necessary to insert 0.1 or 0.22 ohm 5W resistors in series with each source before paralleling the MOSFETs, to prevent current hogging.
R7 and R6 form the feedback network. These set the gain at 27dB. If oscillation is a problem, R7 can be bypassed with a 100pF or so capacitor.
Note the separation of the signal and power grounds in the circuit. The input stage is referenced to the signal ground GNDA. The decoupling capacitors on the supply current are referenced to the power ground (GND). Also note that the output Zobel network is referenced to a third ground labeled GNDIO. GNDIO must be connected to the speaker connection posts' ground terminals, which are then wired directly to the power supply via a thick ground lead. A jumper is provided between GNDA and GND. I found that this jumper had to be cut to give hum-free operation, but your configuration may yield different results.
Power Supply
The power supply for the amplifier has two sections: the low-voltage and high voltage sections. The high voltage section produces an unregulated +/- 38V for the power amplifier. The low voltage section provides +/- 5V for the analog sections (preamp, input selector, etc.) and +5V for the digital sections (MCU, LCD display, etc). It uses a custom-wound transformer, with 30-0-30 @ 4A main windings and 12-0-12 @ 500mA auxiliary windings. A third 0-12 winding is provided for driving the speaker muting relay.
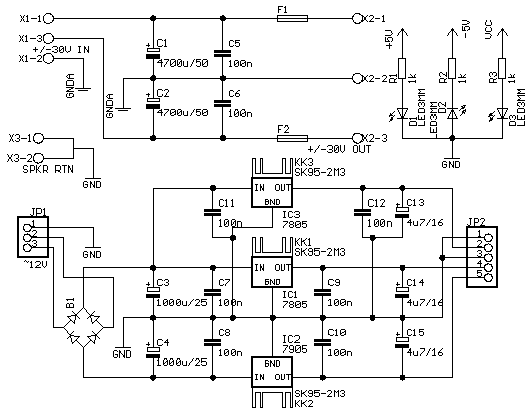
MOSFET Integrated Amp Power Supply
The input voltage (erroneously marked "30V in") connects to a 35A bridge rectifier's + and - terminals. The Bridge's AC terminals go to the extreme ends of a 30-0-30, 4A transformer. The transformer's center tap connects to the middle pin (X1-3). The fuses I used are 5A slow-blow types. The connector labeled JP1 connects to the transformer's auxiliary (12-0-12) windings. The 100nF capacitors C7-C12 should be placed near their respective regulators. C13-15 are tantalum capacitors. Three indicator LEDs are provided to act as indication that one of the supplies is short circuited. They also behave as a minimum load for the regulators.
Speaker Muting
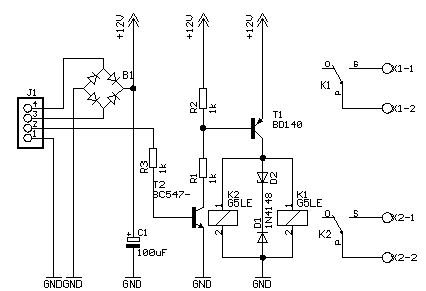
MOSFET Integrated Amp Speaker Muting
The speaker muting circuit presented here uses the MCU to switch on the speakers after a short delay. The amount of delay can be software programmed. At switch-off, the local supply voltage (derived from the transformer's auxiliary 0-12 winding) collapses very quickly, switching off the relay. The headphone jack includes a switch for speaker muting, this is sensed by the MCU (through port RB7), which then switches off the speaker. The circuit's input (J1.2) connects to the MCU's speaker mute relay pin (JP5.3, on the MCU board). A logic high at this pin switches on the relay, and hence the speakers. The relays used should have a 10A DC contact rating, otherwise serious damage can result. The Zener diode used (ZD1) is a 12V type.
Construction
The various PCBs were built on Veroboard, excepting for the power amplifier. These were made on FR4 PCBs, with a good ground plane, etc. The output devices were laid flat on the board, with an aluminium L-section between the devices and the board. This L-section is then bolted onto the heatsink.
The amp was built into a standard amplifier case (from Dexa). It, however, needed significant modification for this amplifier. A large hole had to be cut in the rear to insert the heatsink. Rectangular hole was made in the front panel to insert the LCD panel. The tape selector slots were used to implement the menu and up/down keys. One of the other switch slots was used for the infrared sensor. The cutouts for volume/balance/tone pots were used for front-panel input (RCA jacks), speaker active LED and headphone socket.
http://wiredworld.tripod.com
http://wiredworld.tripod.com
0 comentarii:
Trimiteți un comentariu